Beyond The Batteries: How Electric Trucks Work
Freightliner Electric Trucks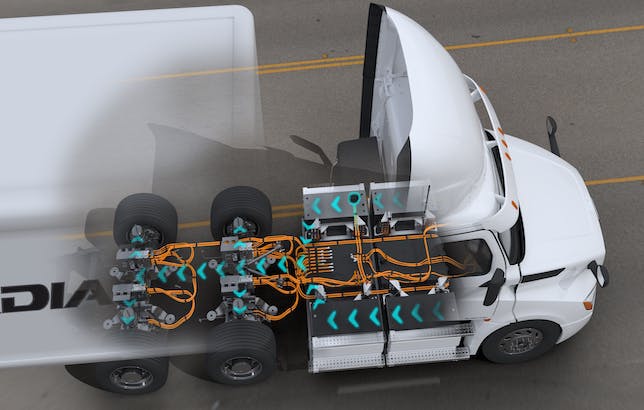
Electric commercial trucks are here, and they continue to rack up real-world miles. But have you ever stopped to think about what’s going on inside of one when it’s on the road? Let’s take a look.
Understanding electric semi trucks isn’t about examining every nut, bolt, wire and battery cell. It’s about looking at the big picture: how the major components of the truck work together to provide optimal efficiency, safety, durability and productivity. That’s the key to understanding the literal power inside – and grasping just how powerful and world-changing these vehicles can be.
FOLLOWING THE CHARGE
Let’s start with the big picture. Here’s an overview of what happens inside the Freightliner eCascadia, from power-on to acceleration to braking.
- When the driver partially turns the key, ions and electrons from the high-voltage batteries are made available to power the truck.
- Once the driver fully turns the key (as if “cranking” the truck), the high-voltage system sends energy to the powertrain.
- Upon being pressed, the accelerator sends a software signal to the inverter, a switch that rapidly opens and closes to convert a direct current (DC) signal into alternating current (AC).
- AC power energizes the electric motor and creates torque. Rotational energy is fed into the electric powertrain, which causes the wheels to turn and the vehicle to accelerate.
- In addition to standard braking, the truck can be stopped via brake recuperation, also known as regenerative braking in passenger EVs. This allows the batteries to recharge. Energy travels from the e-motors to the inverter and all the way back to the batteries.
Despite the major design differences between battery-powered trucks and diesel vehicles, the driving experience remains largely the same– just with less noise, smoother acceleration, more torque and plenty of other benefits that we’ll explore below.
SOFTWARE: THE BRAINS BEHIND THE BRAWN
Another similarity between battery-powered trucks and diesel rigs is their reliance on software. Both types of trucks use software to coordinate all the internal components and systems. The main difference is simply the kinds of components they’re managing.
In the eCascadia, one of the most central software-related parts is the electric common powertrain controller (eCPC), also called the powertrain controller. Let’s say you depress the accelerator about halfway – or 50%. The powertrain controller receives this request to accelerate and immediately checks with other components to determine if giving 50% torque to the e-motor is both safe and efficient for the system.
- If all requirements are met, the powertrain controller allows the inverter to pull energy from the battery and send it to the e-motors to meet the driver’s demand for 50% torque.
- If the powertrain controller determines that giving 50% torque is not ideal (for example, if the truck is stationary or moving slowly), it will reduce torque to the ideal level – for example, 30%.
Of course, the powertrain controller isn’t designed to arbitrarily limit power or torque. It’s engineered to work with a wide range of truck parts to intelligently maximize them – while also being as efficient as possible.
BATTERY INTEGRATION: POWERFUL (AND SMART)
When it comes to batteries, a lot of drivers might just think of the one under the hood of a diesel truck. But in an electric truck, there are several batteries throughout the vehicle. There are also two distinct types:
- High-voltage batteries: These batteries give an electric truck its “go.” In a Freightliner electric truck, the high-voltage batteries are located between the frame rails and power many parts of the vehicle. For example, these batteries drive one to three e-motors (depending on configuration) as well as an electric air compressor, which provides air pressure for the truck’s pneumatic brakes and suspension system.
- Low-voltage batteries: Low-voltage batteries, usually located under the hood of an electric truck, power low-voltage components, such as in-dash controls and various integrated systems.
The battery management system: A key to intelligent power
On their own, batteries are just huge stores of power. However, when controlled by the right software, they’re incredibly smart. In the eCascadia, each battery is optimized via a battery monitoring system (BMS). The BMS is a controller that uses specialized software to keep tabs on what’s happening inside each battery and help them operate efficiently.
Thermal management: Keeping batteries happy
The BMS pays attention to charge and temperature within each battery cell, so it can ensure that all systems run safely and efficiently. For example, if one battery gets too warm, the BMS calls on the truck’s thermal management system to quickly reduce the battery’s temperature via liquid cooling. In cold environments, the BMS can use the same system to keep batteries warm and performing their best.
Designed for durability with fewer moving parts
Battery-powered trucks also have fewer parts – especially moving parts – which can help minimize maintenance in the long run. And it’s not just the e-motor. In the eCascadia, a 2-speed transmission replaces the need for a more complex 12-speed transmission that one might find in a diesel truck. In short, Freightliner electric trucks are engineered with simplicity and durability in mind.
BRAKE RECUPERATION: ENERGY OUT – AND BACK IN
For electric trucks, energy is a two-way street. Not only can the batteries and inverter power the e-motor, which ultimately drives the e-axle and wheels. The entire system can work in reverse. The driver can quickly initiate a process called brake recuperation. Brake recuperation allows the e-motor to convert mechanical motion back into electrical charge that can be stored in the batteries. In a world where efficiency matters, brake recuperation isn’t just smart. It’s the future.
SEE FREIGHTLINER ELECTRIC TRUCKS ON THE ROAD
There’s a lot more to discover. Check out our eM2 and eCascadia to see how electric truck technology is racking up miles in the real world.